BLT Introduces BLT-Ti₂AlNb – a new alloy for metal 3D printing
The alloy is resistant to high temperatures and is suitable for the production of lightweight and durable structures
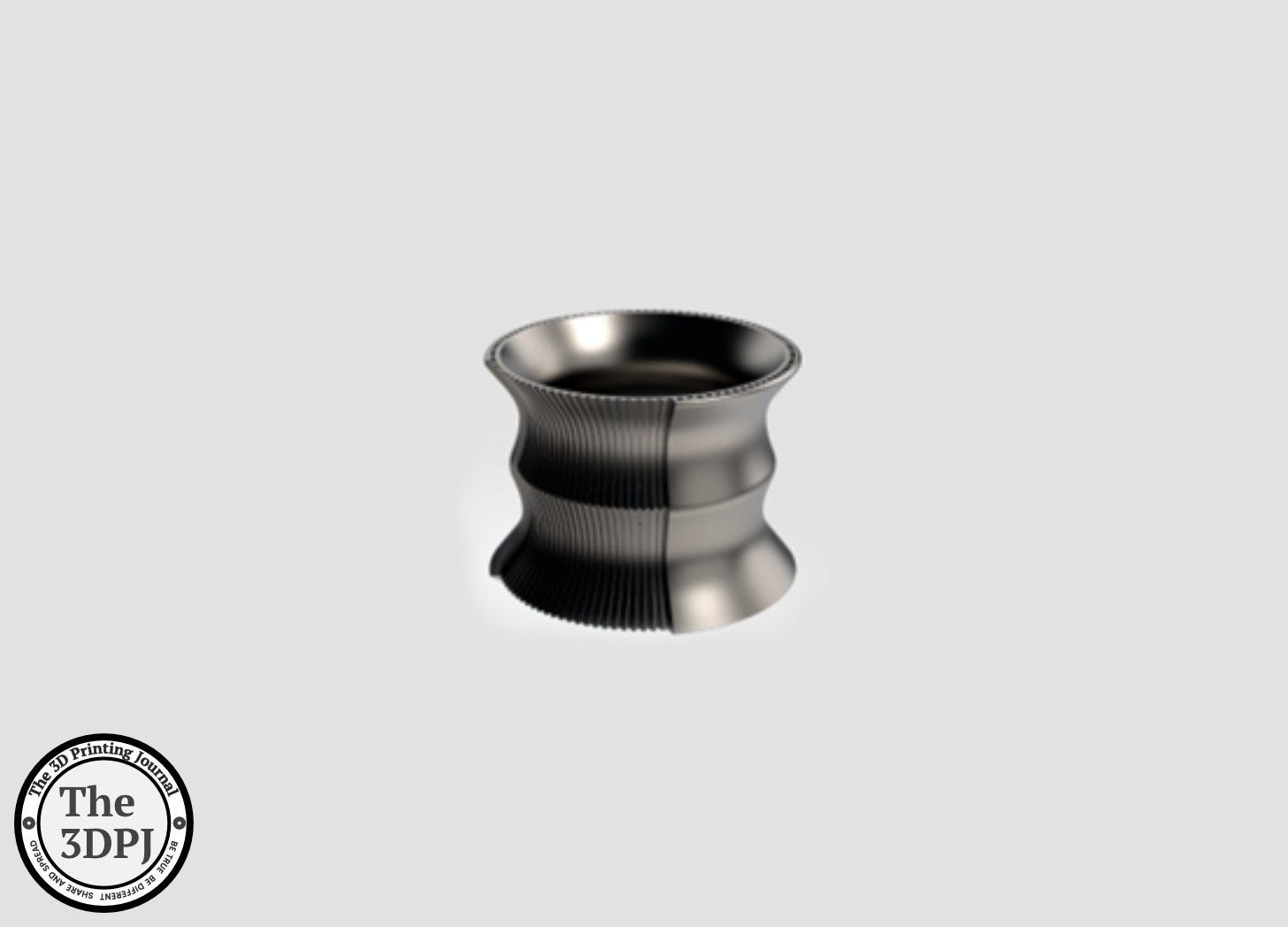
The Chinese industrial 3D printer manufacturer - Bright Laser Technologies (BLT), has announced the launch of a new metal alloy, BLT-Ti₂AlNb. This material is designed for applications in the aerospace and automotive industries. The company claims that the material is ideal where high-temperature resistance, low weight, and structural applications are required. Additionally, it boasts excellent oxidation and corrosion resistance.
While traditional methods of producing parts made from Ti₂AlNb are characterized by the alloy's poor plasticity at room temperature and thermal deformability, BLT claims that the rapid development of additive manufacturing technology offers a new path to overcoming these challenges. BLT uses advanced inert gas atomization technology to produce the powder, combined with optimized processing techniques. This significantly reduces the occurrence of satellite powder. This, according to BLT, ensures the consistent mass production of high-quality BLT-Ti₂AlNb powder.
The nominal chemical composition of BLT-Ti₂AlNb powder is Ti-22Al-25Nb, and the product specification is 15-53μm. The alloy exhibits excellent properties both at room temperature and high temperatures, with low density and high-temperature oxidation resistance. It can withstand extended use at temperatures ranging from 800℃ to 900℃. After heat treatment, parts made from BLT-Ti₂AlNb powder achieve impressive mechanical properties, with a tensile strength of 250-270 MPa, a yield strength of 140-160 MPa, and an elongation of 38.8%-42.8% at a high temperature of 900℃.
To demonstrate the material's capabilities, BLT produced a demonstration sample of a flow channel. The sample features a typical structure of an actively cooled liquid engine, with dozens of rectangular flow channels designed in the internal and external walls of the part. The structure is compact, with the thinnest wall being just 1 mm thick, showcasing the ability of BLT-Ti₂AlNb material to form via selective laser melting (SLM).
To achieve optimal results, BLT meticulously optimized process parameters, including scanning speed, laser power, scan spacing, and preheating temperature, to define the appropriate process window for preparing Ti₂AlNb-based alloy components.
These refined parameters are now applied across all commercially available BLT devices, enabling the production of dense, crack-free parts with consistent quality.
Source: www.xa-blt.com