Metal 3D printing helped British Olympians win medals in Paris
Renishaw technology assisted the team in securing eight medals in track cycling events
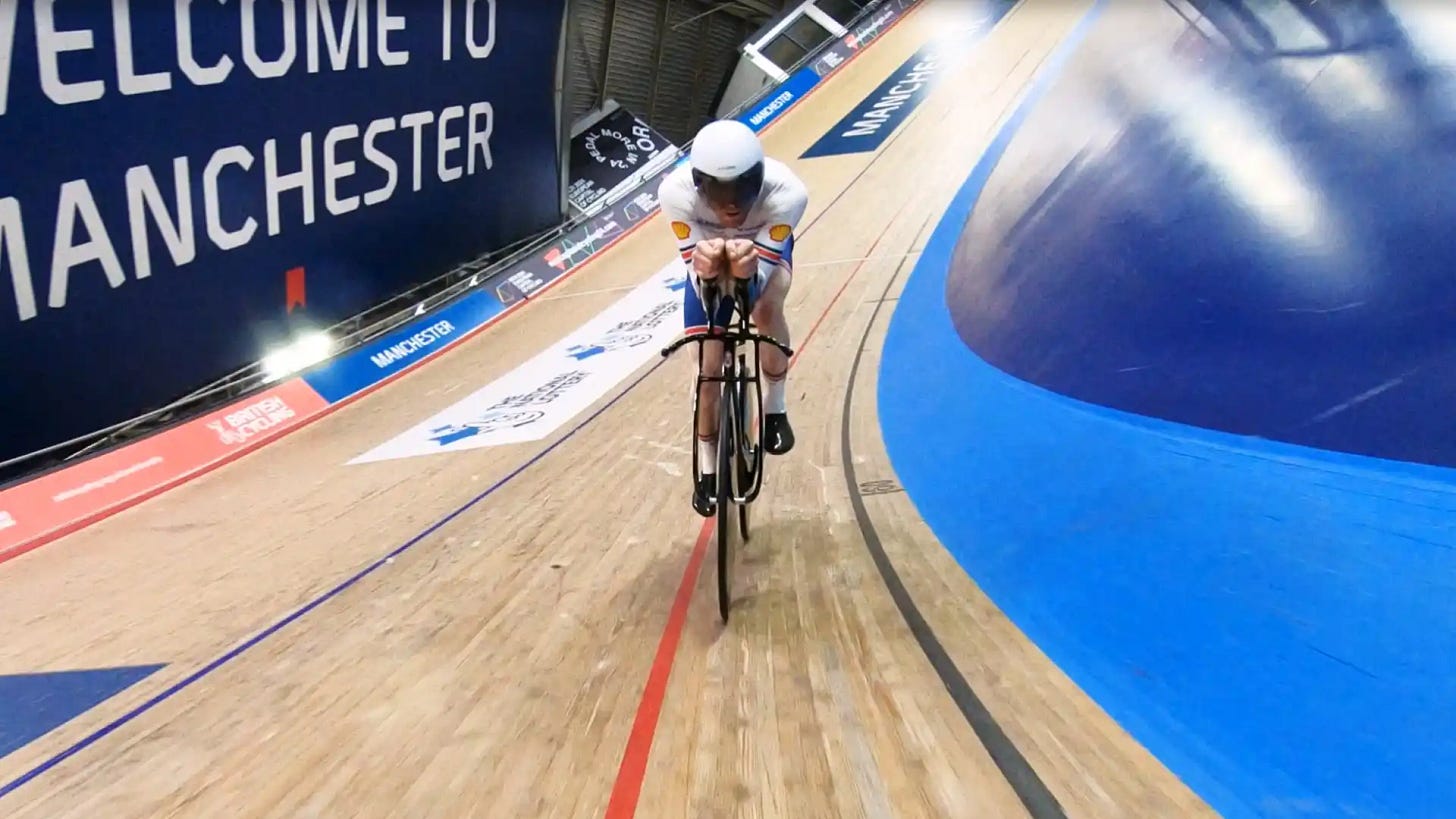
Renishaw has been supporting British sports teams for many years—particularly cycling teams—in achieving better sports performance. A recent notable example is the use of metal additive manufacturing technology to produce a range of components for the track bikes of British Olympians. Thanks to the implemented innovations, the British cycling team won eight medals—including one gold. The gold medal was secured by the women's team, who also set a world record.
Renishaw produced parts such as an aerodynamic crankset, dropouts, a seat post clamp, and a saddle seatpost.
As for specific examples, the seatpost had a hollow center and a backward-tilted design, allowing airflow through the middle of the bike. The crankset, on the other hand, was designed with a variable lattice structure, denser in areas likely to endure greater stress, and less dense where it could afford to be lighter.
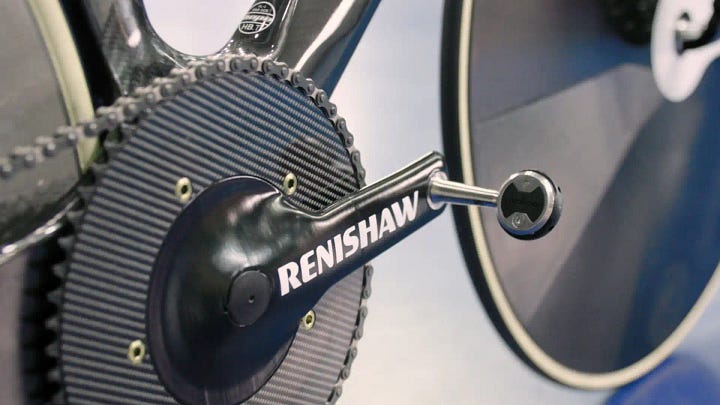
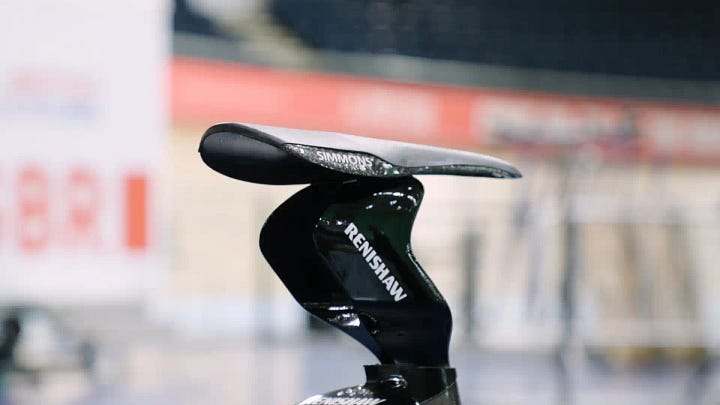
In total, Renishaw produced over 1,000 parts for 32 track bikes and spare parts.
Renishaw collaborated with British Cycling during the Tokyo 2020 Olympic Games, and the UK's national cycling governing body wanted to leverage that success for this year's Games. The shorter lead time between the Tokyo Olympics (held in 2021 due to the Covid-19 pandemic) and the Paris Olympics meant that the British team faced significant time constraints for this year's Summer Olympics.
The carbon fibre parts produced using traditional machining methods for the Tokyo bike met all the requirements we had, but time constraints for the Paris bike meant that this method was no longer viable for some bespoke parts. After seeing the benefits of AM and what it helped us achieve on the Tokyo bike, we knew it could be a manufacturing method to explore further.
explained Dr Oliver Caddy, Lead Project Engineer at British Cycling.
Once it was determined that the British Cycling team couldn’t produce the crankset cores and seatposts in carbon fiber within the required shorter timeframe, we began creating additively manufactured prototypes in plastic. Additive manufacturing enabled us to create complex geometries that removed unnecessary weight while providing the strength athletes needed to reach racing speeds. To develop a more aerodynamic seatpost, engineers designed more freeform geometries to hollow out the part as much as possible, which could not have been achieved using traditional methods.
said Ben Collins, Lead Additive Manufacturing Applications Engineer at Renishaw.
Source: www.renishaw.com